Procesos
de producción
Extracción
La amplia zona reúne las mejores condiciones de mineralizaciones explotables. Las concesiones de arenas caoliníferas se encuentran en los términos de Poveda de la Sierra y Peralejos de las Truchas, a unos 210 Km. al Noreste de Madrid, y las arenas feldespaticas se situan en la misma zona y en los términos municipales de Taravilla y Atienza, al noroeste de la provincia de Guadalajara.
La explotación minera se realiza con los más modernos procedimientos operativos y utilizando maquinaria puntera , lo que permite un aprovechamiento óptimo de las distintas composiciones mineralógicas que se dan en nuestras explotaciones.
Tratamiento
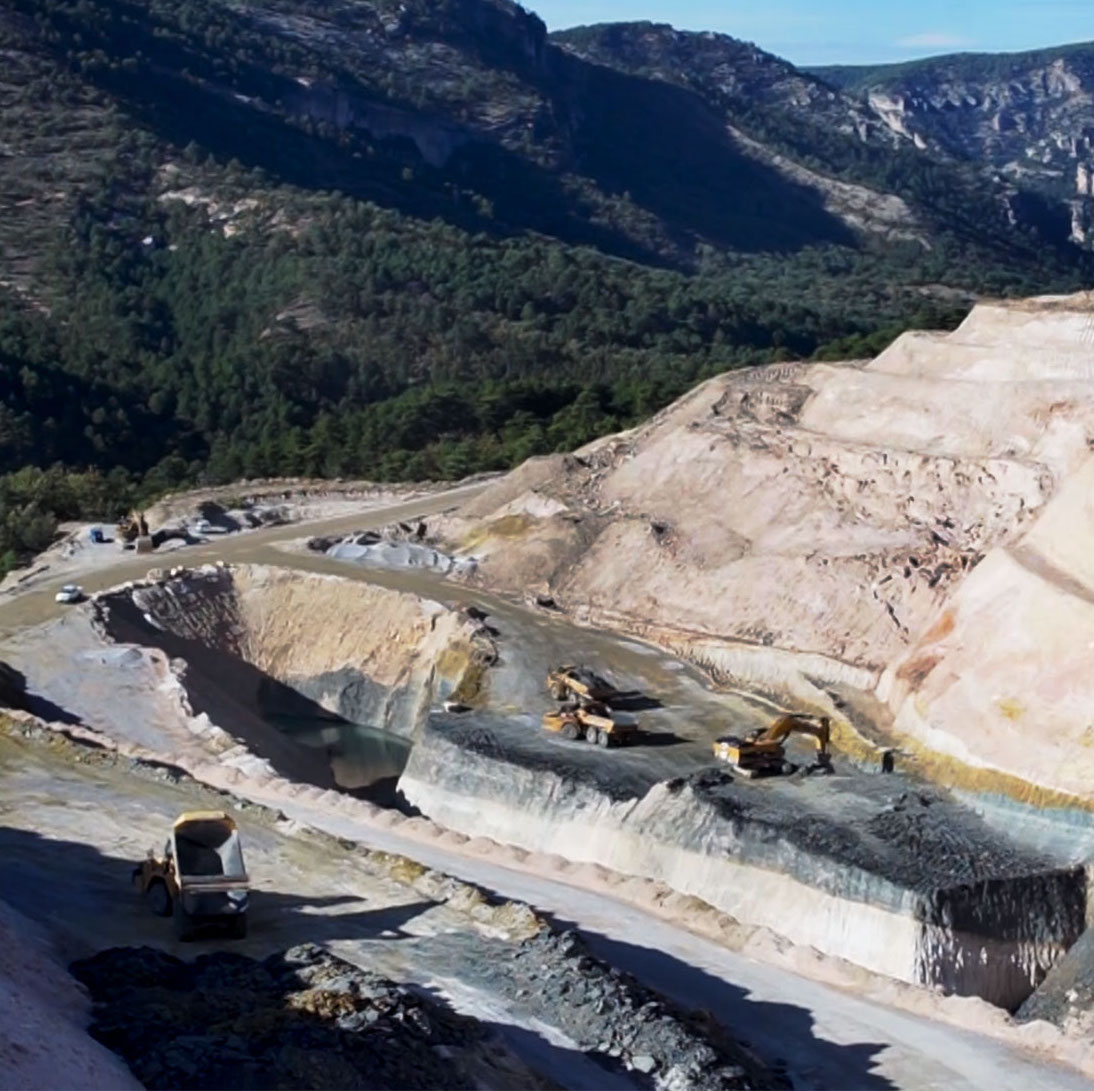
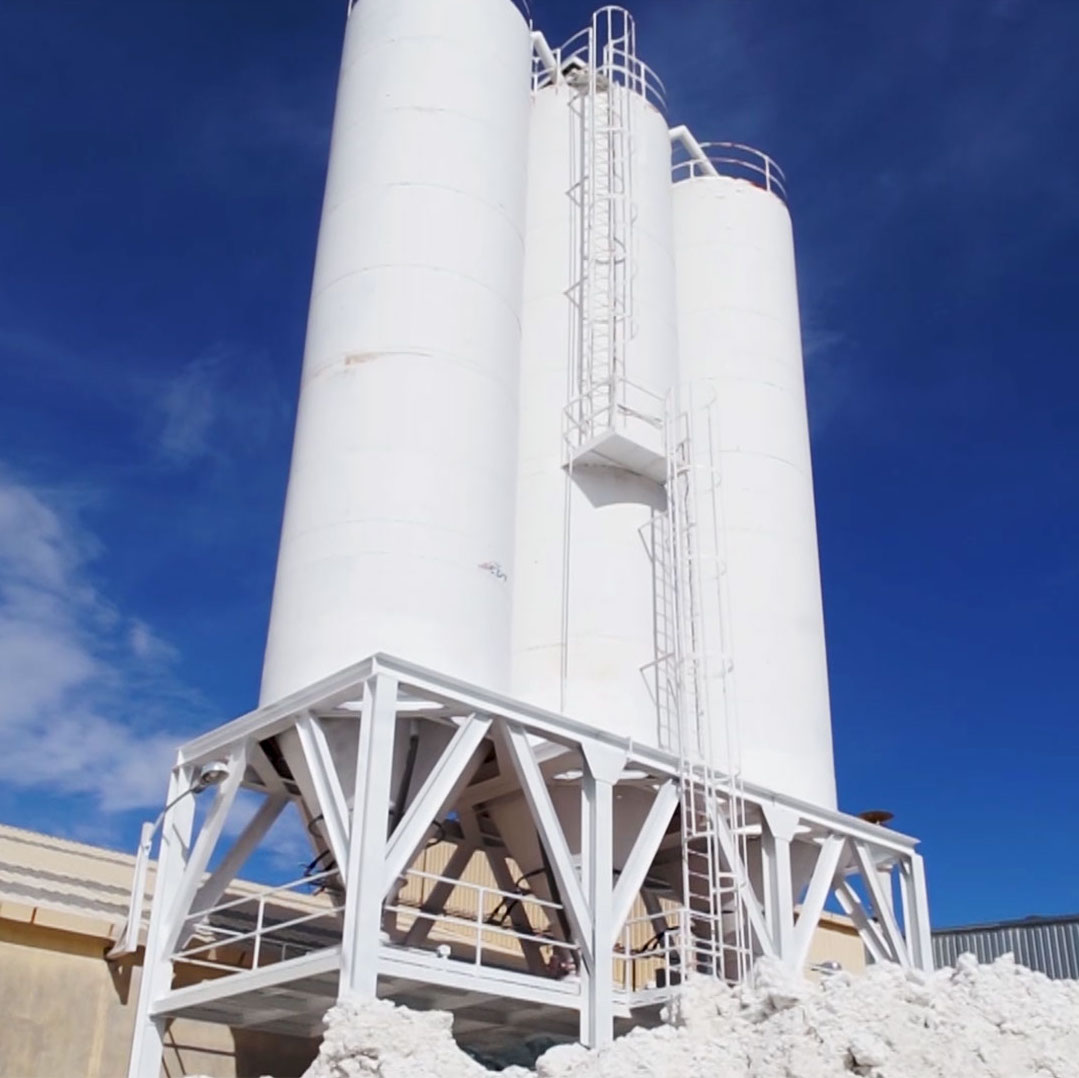
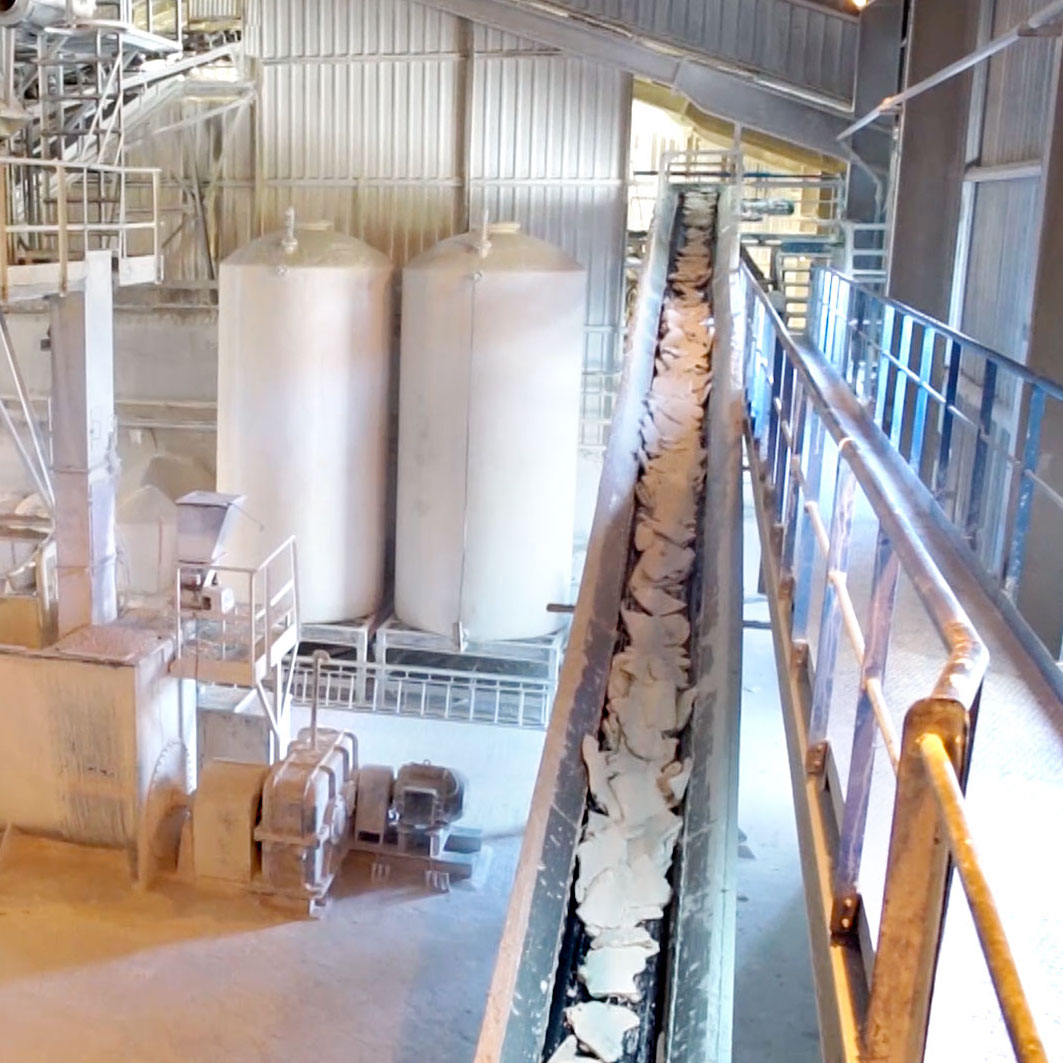
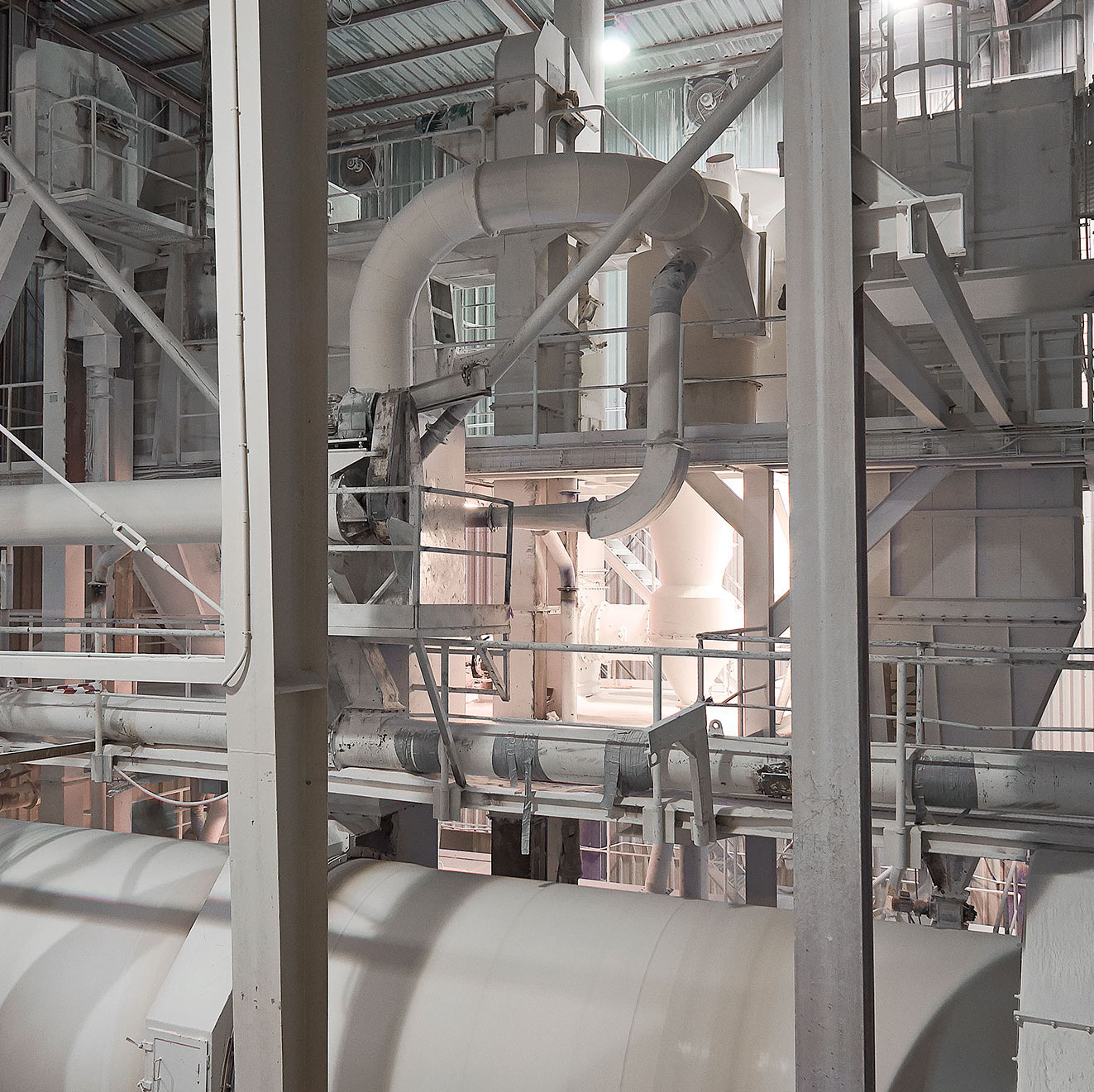
Caolín
El caolín, también llamado China Clay, es una roca o sedimento que contiene cierta proporción (>15%) de caolinita. La caolinita posee la siguiente fórmula química Al2O3.2Si02.2H2O. Se distingue de otras arcillas principalmente por su blandura, blancura y fácil dispersión en agua y otros líquidos.
Después de la separación de las arenas de sílice, la pulpa de caolín pasa por diferentes baterías de ciclones, donde se producen las diferentes calidades de caolín.
Tras un proceso de concentración de la pulpa, pasan a la sección de filtroprensado, que permite obtener tortas de caolín.
Las tortas son troceadas y mediante diferentes procesos de secado utilizando gas natural. Se obtiene un caolín granulado o bien en polvo que es almacenado adecuadamente para su posterior carga en cisternas o en camiones.
Fichas de Caolines
Algunos usos y aplicaciones CAOLÍN
Sílice
La sílice se ofrece seca y clasificada o micronizada, para ello pasa por un proceso de secado en secaderos rotativos con gas, seguidamente pasa por un proceso de cribado para obtener la granulometría deseada con diferentes cortes intermedios de 0 mm a 4 mm, o bien pasa por un proceso de micronización consistente en molinos continuos vía seca, , en los cuales ya obtenemos los diferentes cuarzos con granulometrías que oscilan entre las 125 micras y las 10 micras.
Una parte vital en todo el proceso de tratamiento es la realización de los ensayos correspondientes a cada etapa del proceso de producción. Se analiza el mineral tanto en el yacimiento como en la zona de almacenamiento.
Para los estudios de investigación y control se cuenta con los medios técnicos más modernos, así como con un personal altamente cualificado.
Una vez finalizada la cadena productiva, la materia prima está lista para su posterior distribución y para ello Caobar le ofrece a sus clientes la expedición más adecuada: granel en cisternas o bien en la gama de productos envasados en sacos o big-bags.